Aerodynamic Efficiency
Enhance Durability, Aerodynamics and Reduce Weight with Generative Design
Over several hundred iterations, Parallel Pipes’ AI was able to improve the drone’s aerodynamic efficiency and durability, increasing its lifespan and flight performance. Through enhanced generative design a combination of material changes, topology optimizations and shape modifications were proposed which led to a design improved in nearly every aspect.
Challenge
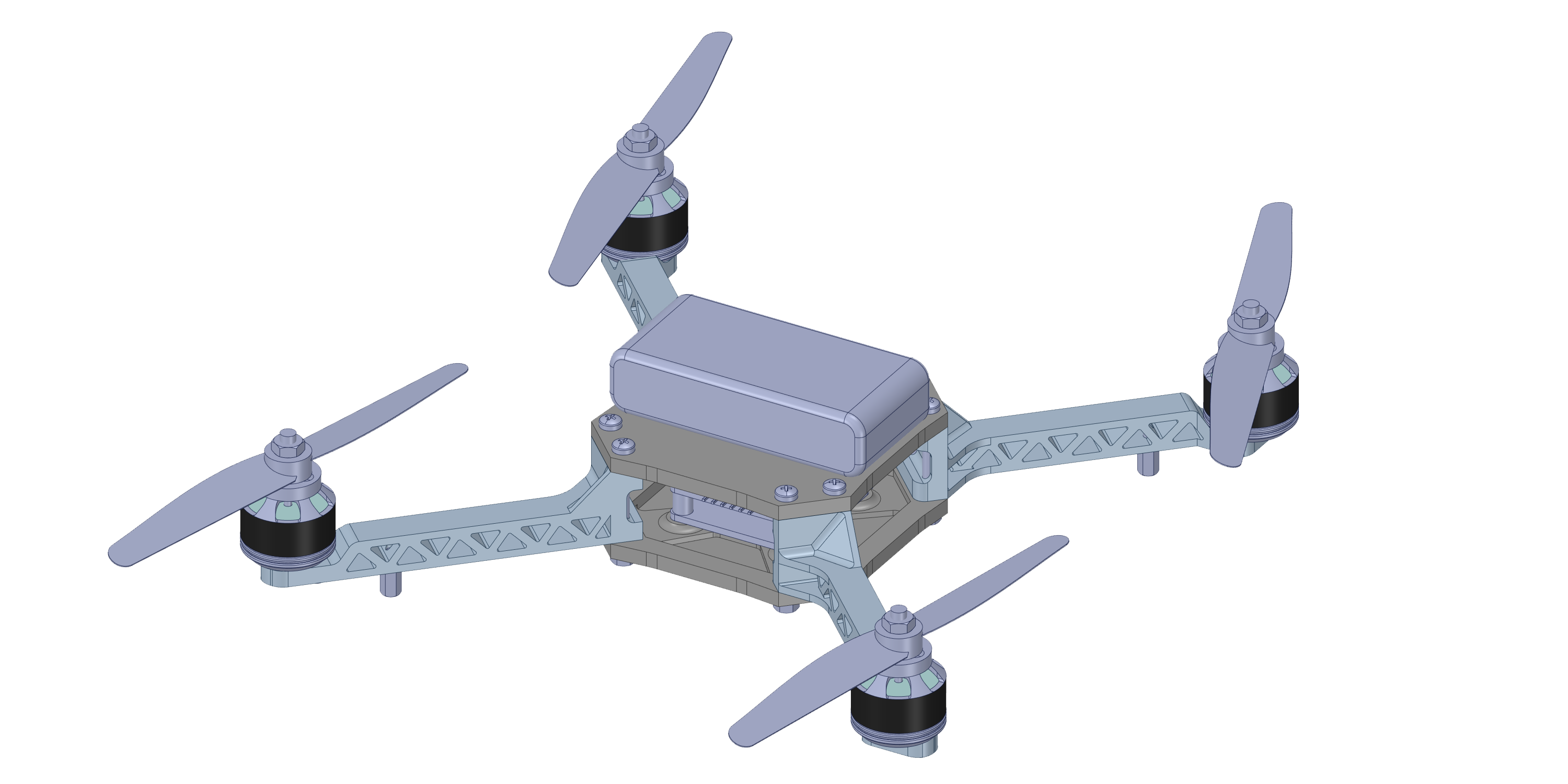
Quadcopter drones are one of the more common types on the market today, and are used for a wide variety of purposes such as picture and video capture, package delivery, crop dusting and seed dispersal.
The engineers designing the quadcopter seen in figure 1 wanted their drone to be both aerodynamically efficient, and able to withstand the stress of both flight and moderate collisions. To save time and money, they chose Parallel Pipes so they could jump right through to the end of the prototyping phase and get their product to market as soon as possible.
Design Goals
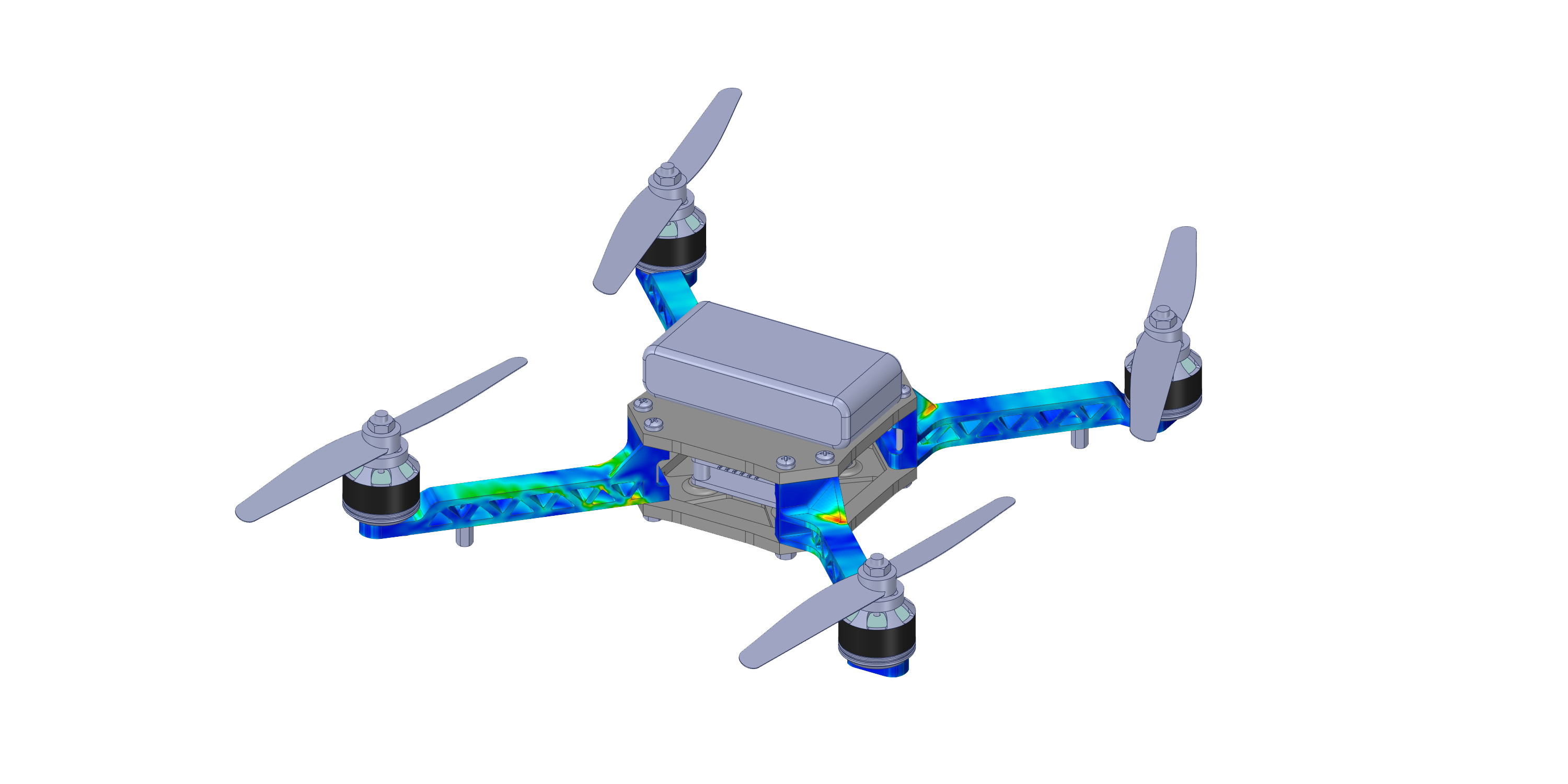
stress and fatigue
Design goals for the project included weight reduction, but also to improve durability and aerodynamic efficiency. Stress in the initial design, shown in figure 2, would lead to a mean time to failure of around 1.5 years of heavy usage. This necessitated using Parallel Pipes’ method of enhanced generative design, to automatically optimize for several different factors all at once.
AI-Guided Optimization
The blades and arms were allowed to change materials from different alloys of aluminum and different types of PVC, but only the arms were allowed to have their shape changed. As seen in figure 3, stress on the arms was reduced dramatically by the changes to the arm’s shape through topology optimization and reinforcement, and both the blade and arm materials. Mean time to failure was doubled to an estimated 3 years of heavy usage.
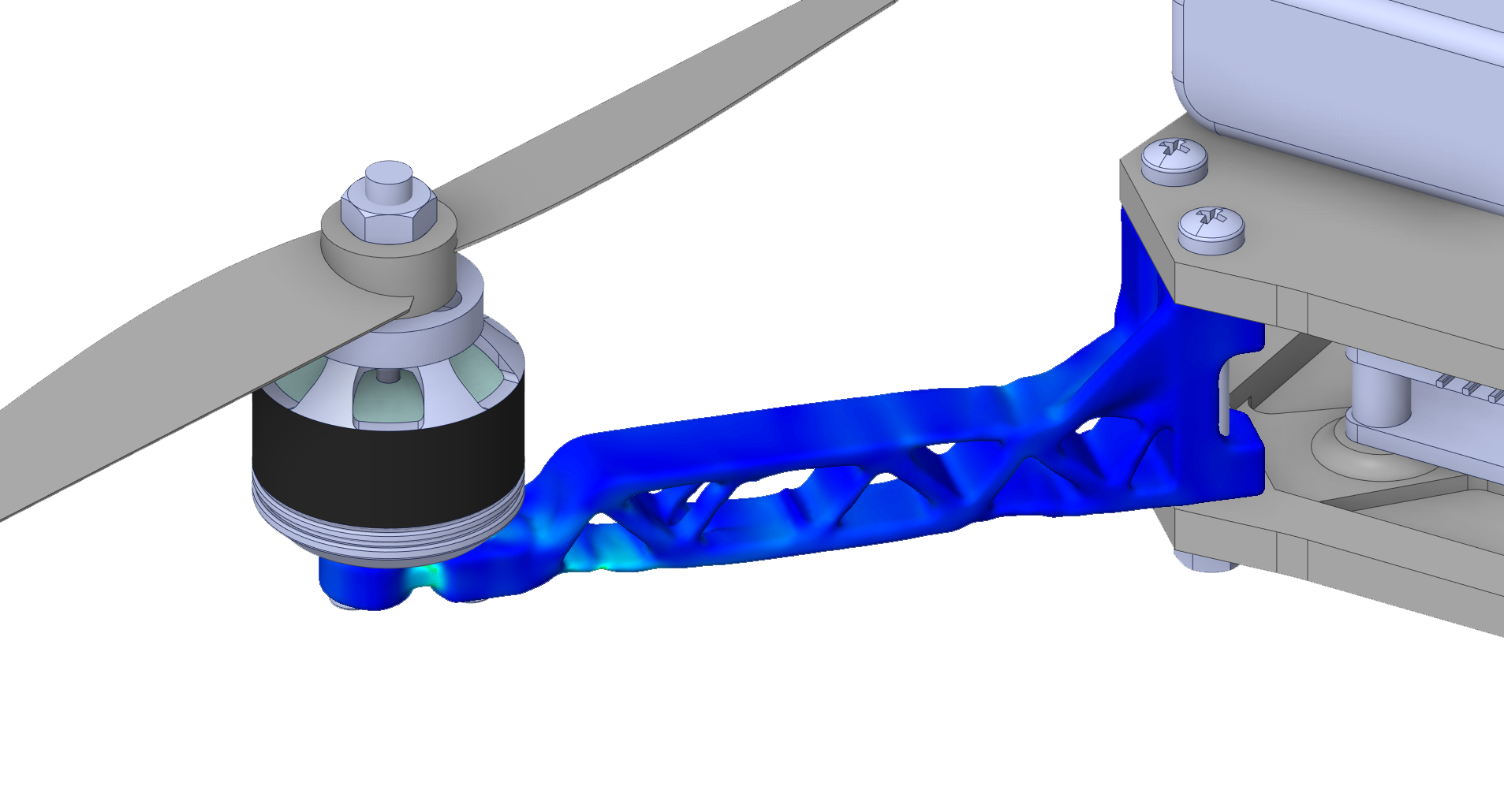
Both shortening the arm length and adding slight curvature to the arms improved the drone’s overall aerodynamic efficiency, as seen in figure 4. The shape optimization also helped increase expected lifespan, by reducing lifetime stress during flight.
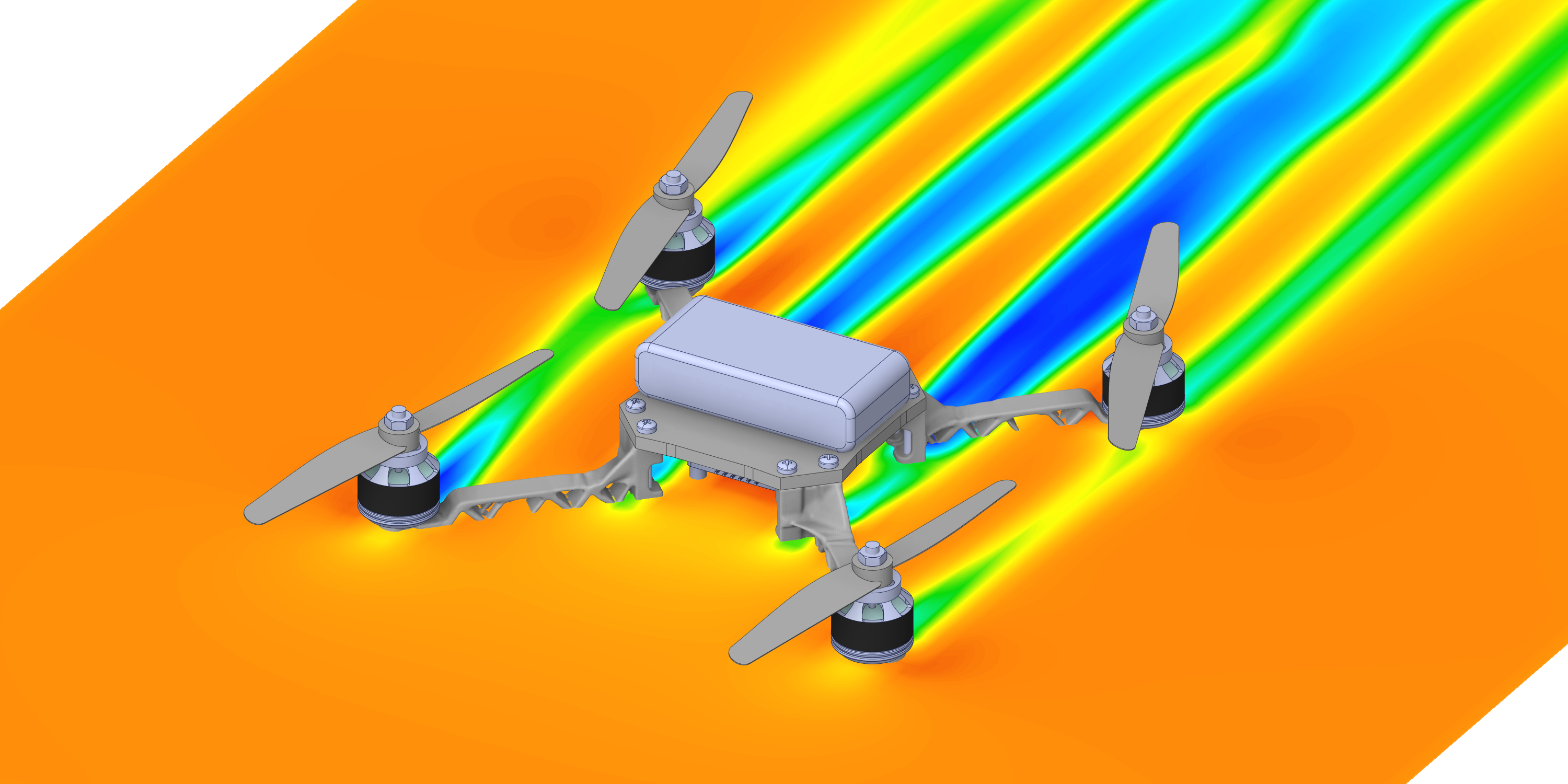
Results
Over several hundred iterations, Parallel Pipes’ AI was able to improve the drone’s aerodynamic efficiency and durability, increasing its lifespan and flight performance. Through enhanced generative design a combination of material changes, topology optimizations and shape modifications were proposed which led to a design improved in nearly every aspect.